Optimized Heat Treating: A Success Story
- 06/27/2025
- USMarketing
- Uncategorized
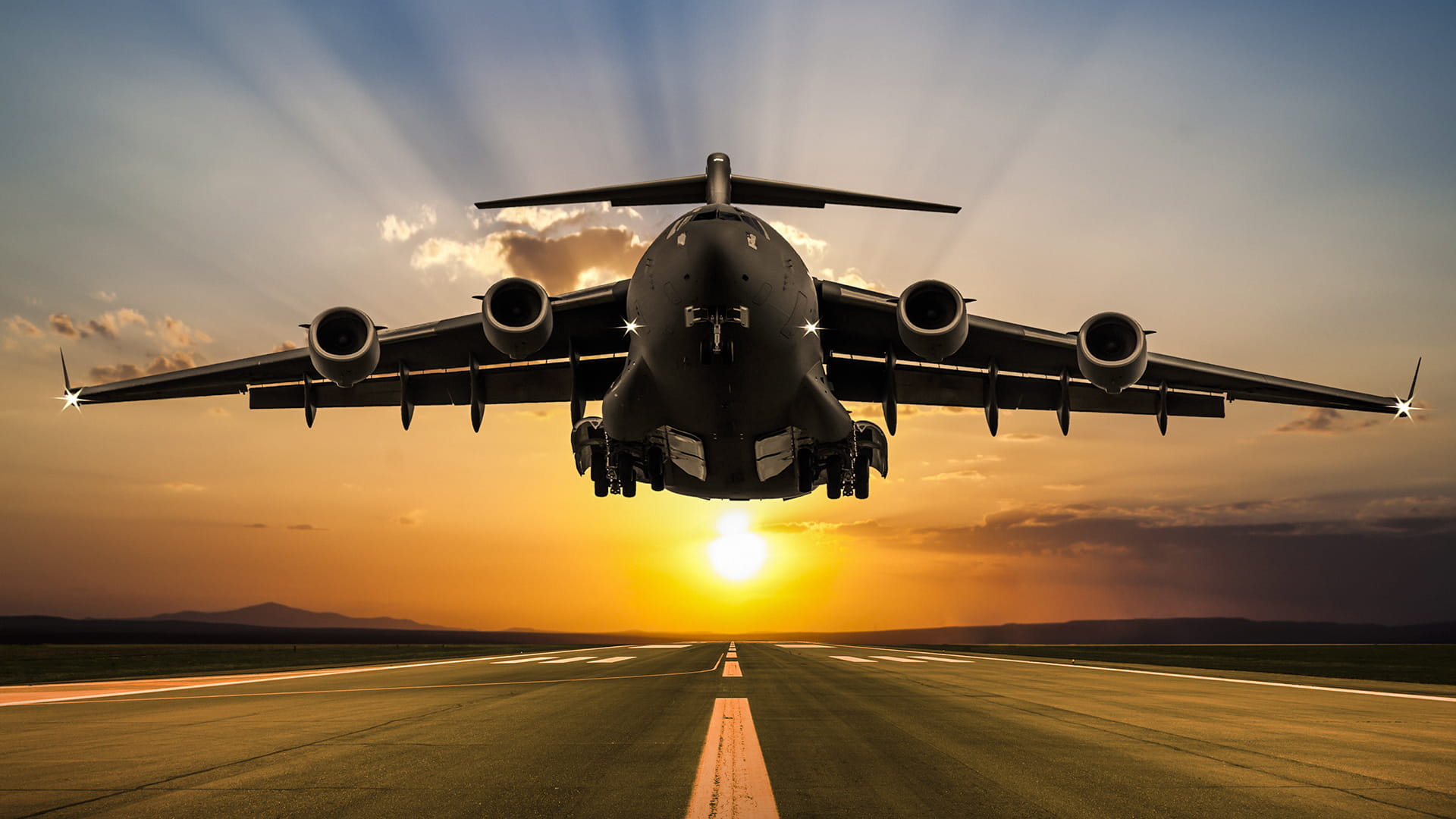
REDUCING COSTS DURING HEAT TREATING & BRAZING PROCESSES
Connecticut, USA | June 27, 2025 | 6.5 min read
Collins Aerospace is an American technology company and global leader specializing in advanced aerospace systems and avionics, serving commercial, business, military, space, and airport sectors.
They design and manufacture avionics, flight control systems, and communication solutions for commercial and military aircraft. Collins Aerospace also develops innovative interiors that enhance passenger comfort and operational efficiency, along with software that streamlines data management for airlines, airports, and maintenance teams.
VESCO, part of the Busch Group, provides its expertise in installation and service for vacuum systems used in the heat treating and brazing of superalloys, processes trusted by leading aerospace manufacturers such as Collins Aerospace, which utilize Busch Vacuum Solutions technology.
Superalloys are preferred in aerospace for their exceptional resistance to high temperatures and corrosion. By using a dry vacuum system with reliable pumping speeds, Collins Aerospace has reduced maintenance costs and improved production efficiency by 80%.
Heat Treatment at Collins Aerospace
The alloy is heated in a vacuum furnace, a sealed chamber where most air and reactive elements are removed to prevent oxidation and contamination.
A vacuum system connected to the chamber extracts oxygen and nitrogen, creating a clean environment for precise material processing.
Common vacuum furnace processes include vacuum brazing, annealing, precipitation hardening, tempering, normalizing, and stress relieving, each tailored to the specific needs of the material being processed.
Vacuum Brazing Process
Collins Aerospace uses a very precise process that involves several key steps:
1. Clean: Remove dirt or impurities from all parts before brazing.
2. Assemble the Braze: Attach the filler metal (foil, paste, powder, or thread) to the parts.
3. Position: Place the parts on the furnace frame.
4. Heat: Use a vacuum furnace to heat the parts until the filler metal melts.
5. Allow Filler to Flow: Capillary action pulls the liquid filler into the joints between each piece.
6. Cool: Allow the filler to solidify and form a bond between the parts.
7. Inspect: Visually inspect parts for any issues.
8. Test: Perform any final tests on all parts.
Overcoming Challenges
Collins Aerospace previously used an oil-sealed rotary piston pump (OSRP) in its vacuum brazing process but faced several limitations. The pump’s large oil reservoir managed soot by-products, which created an oil waste stream that required time-consuming disposal about 3 times a year.
In addition to being labor-intensive and adding operational costs, the OSRP struggled to deliver consistent pump-down times and stable vacuum levels, both critical for high-precision brazing. Its noisy operation also contributed to an unpleasant work environment.
To improve reliability, efficiency, and overall working conditions, Collins Aerospace sought a cleaner, more advanced vacuum solution.
The Right Team, the Right Solution
To improve their vacuum brazing process, Collins Aerospace turned to VESCO, part of the Busch Group, for expert guidance and support. The VESCO team assessed the existing system and, in collaboration with a Busch Group representative, recommended replacing it with the Busch COBRA dry screw COMBI vacuum system, a cleaner, more efficient solution tailored to their needs.
COMBI vacuum pump units are the perfect vacuum generators to meet the precise requirements of Collins Aerospace’s manufacturing process. These compact systems combine a dry screw vacuum pump and a rotary lobe vacuum booster into a single unit. The working pressure and pumping speed can be finely tuned to match virtually any process condition or pumped medium thanks to the customization from the numerous configuration options.
COBRA vacuum pumps maintain high pumping speeds across the entire vacuum range while operating with exceptional efficiency. Their oil-free, contact-free design minimizes wear and significantly reduces maintenance requirements, making this the ideal solution for Collins Aerospace.
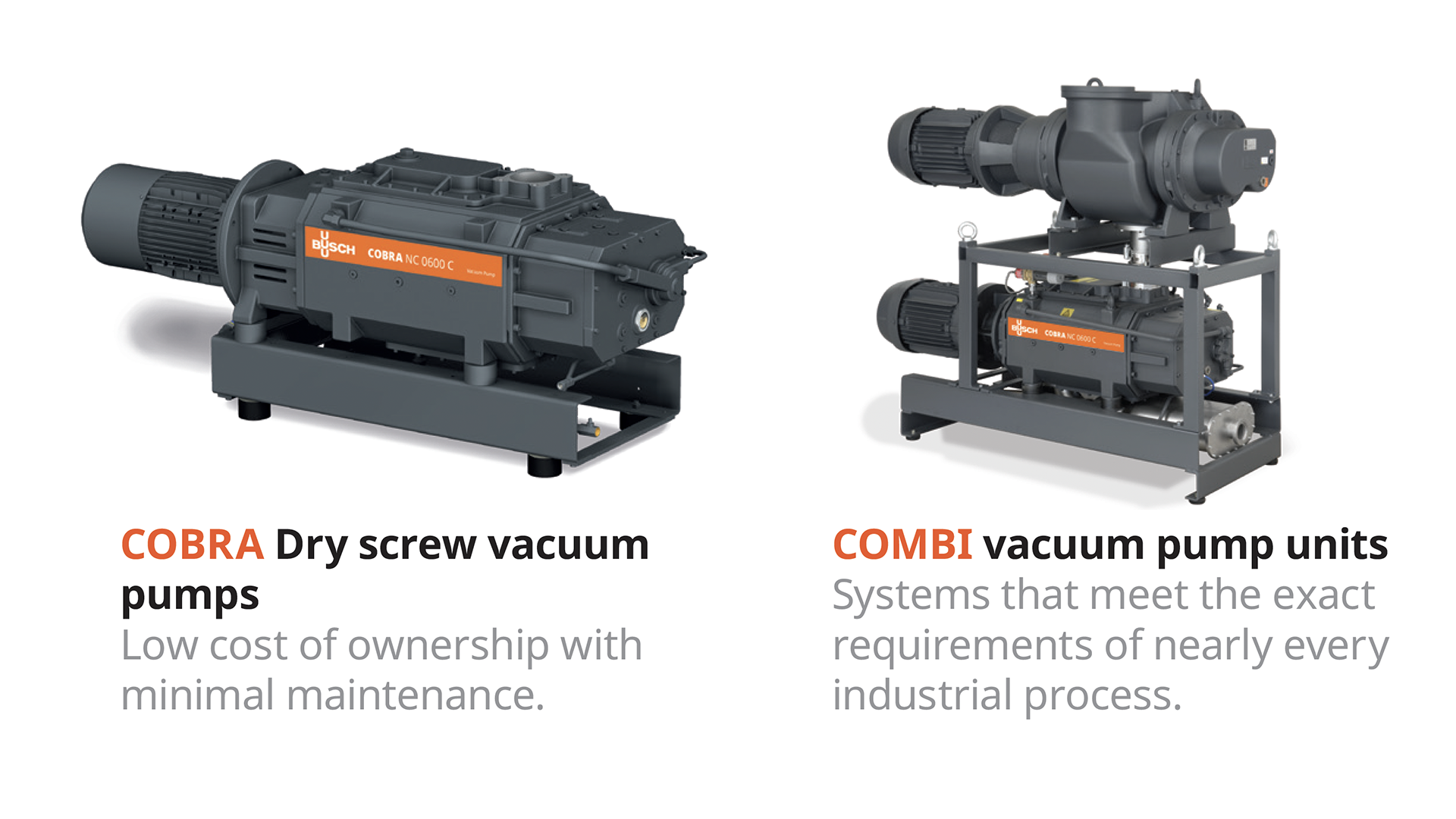
Since installing the Busch COBRA COMBI unit, the Collins Aerospace team has experienced several significant advantages:
Faster pump down: The new unit allowed their furnace to pump down 80% faster, resulting in quicker production cycles.
Increased production: With the improved pump-down cycle, the customer achieved higher production throughput.
Reduced noise: The noise level significantly decreased, making an easier work environment.
Consistent performance: Reliable pump-down times and stable vacuum levels enhanced process consistency.
Reduced maintenance: The oil-free and contact-free design requires far less upkeep than the previous system.
Cost savings: Eliminating oil disposal and related maintenance tasks cut operating costs.
Keeping it simple: Maintenance has been simplified by eliminating filter replacements and valve deck adjustments.
Streamlined operations: No more 55-gallon oil drum storage or handling.
VESCO Vacuum Expertise
These improvements were made possible by the expert team at VESCO, who managed the installation and integration of the Busch COMBI system. VESCO continues to support Collins Aerospace through preventative maintenance programs that help ensure long-term efficiency, reliability, and vacuum system performance.
“Thanks to the Busch vacuum supplied by VESCO, we can significantly increase our production cycles and lower our maintenance costs.”
– Joe Billante, Maintenance Manager
Looking to improve vacuum furnace performance? Contact the VESCO team today!