Vacuum Furnace Inspection Checklist Before Purchase
- 02/05/2025
- USMarketing
- Uncategorized
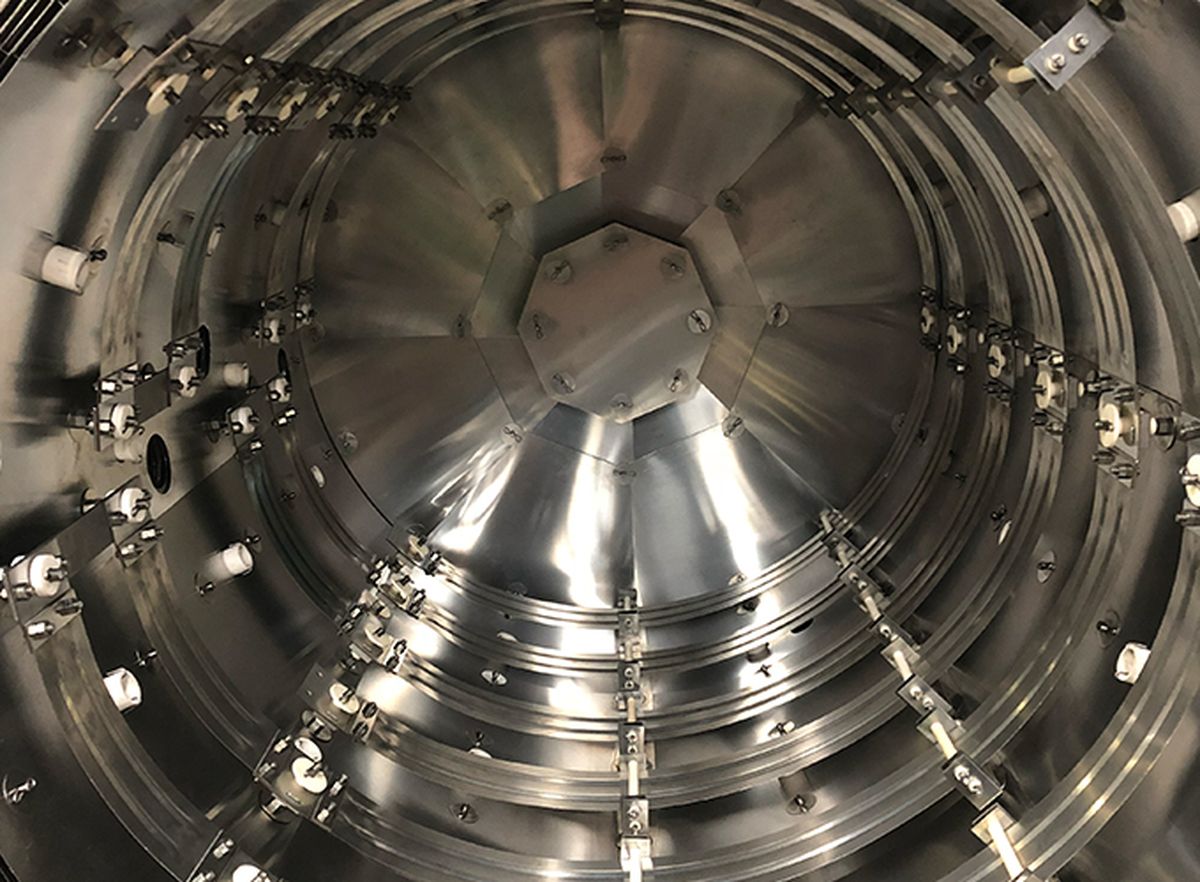
Vacuum Furnace Inspection Checklist
Connecticut, USA | Feb 05, 2025 | 6.5 min read
Purchasing a used vacuum furnace can be a cost-effective solution for many businesses. However, it’s crucial to conduct a thorough inspection to ensure you’re making a wise investment. Here’s an essential checklist to guide you through the process:
1. Visual Inspection
Start with a comprehensive visual inspection. Look for any signs of wear and tear, corrosion, or damage to the furnace body, doors, and seals. Check for any visible leaks or cracks that could affect the furnace’s performance.
2. Vacuum System
Examine the vacuum system components, including the vacuum pumps, gauges, and valves. Ensure that the pumps are in good working condition and that there are no leaks in the system. Verify that the vacuum gauges are accurate and functioning properly.
3. Heating Power and Elements
Inspect the heating elements for any signs of damage or excessive wear. Ensure that they are evenly distributed and securely mounted. Check the electrical connections and insulation for any signs of deterioration. Assess the heating power to ensure it meets your process requirements.
4. Temperature Control System
Test the temperature control system to ensure it is functioning correctly. This includes checking the thermocouples, temperature controllers, and any associated software. Verify that the system can accurately maintain and control the desired temperatures.
5. Operating Temperature and Temperature Uniformity
Ensure that the furnace can achieve and maintain the required operating temperatures for your processes. Check for temperature uniformity within the chamber to ensure consistent results. This is particularly important for processes requiring precise thermal conditions.
6. Chamber Condition
Examine the interior of the furnace chamber. Look for any signs of contamination, residue, or damage to the chamber walls. Ensure that the insulation is intact and in good condition. Check the condition of the hearth and any fixtures inside the chamber.
7. Process and Material Compatibility
Verify that the furnace is compatible with the materials and processes you intend to use. This includes ensuring that the furnace can handle the specific thermal and chemical requirements of your applications.
8. Dew Point, Cooling and Gas Management
Check the dew point to ensure it meets your process specifications and assess the gas cooling rate to confirm it aligns with your cooling requirements. Proper gas management is crucial to maintaining product quality. Make sure that test equipment for monitoring gas quality is properly installed on the furnace.
9. Furnace Classification (for Aerospace Applications)
If you are in the aerospace industry, verify the furnace classification to ensure it meets the necessary standards and regulations. This includes checking the temperature uniformity and control systems to ensure compliance with industry requirements.
10. Pump-Down Time and Vacuum Level
Evaluate the pump-down time and the achievable vacuum level. Ensure that the furnace can reach and maintain the required vacuum levels for your processes efficiently.
11. Safety Features
Verify that all safety features are intact and operational. This includes emergency shut-off switches, alarms, and interlocks. Ensure that the furnace meets all relevant safety standards and regulations. Include water system safety features, pressure, temperature, flow.
12. Loading and Load Fixturing
Assess the loading mechanisms and load fixturing to ensure they are suitable for your materials and processes. Proper loading and fixturing are essential for achieving consistent results and preventing damage to the furnace.
13. Plant Layout and Ergonomics
Consider the plant layout and ergonomics of the furnace. Ensure that the furnace can be integrated into your existing setup and that it is easy to operate and maintain. Good ergonomics can improve efficiency and reduce the risk of operator error. Ask: does it fit into the new premises without major civil engineering – doorways etc. and is the floor sufficiently load bearing to take the weight.
14. Maintenance Records
Request the maintenance records from the previous owner. These records can provide valuable insights into the furnace’s history, including any repairs or replacements that have been made. A well-maintained furnace is likely to be in better condition.
15. Operational Test
If possible, conduct an operational test of the furnace. This will allow you to observe the furnace in action and identify any potential issues with its performance. Pay attention to the vacuum levels, temperature stability, and overall operation. Consider a live test before purchase. Conduct a benchmark test against the specification requirements. Also use this test to ensure the reinstalled furnace is as good as its previous install.
16. Documentation
Make sure all necessary documentation is readily available, including the user manual, wiring diagrams, and any relevant certifications, as proper documentation is essential for the safe and efficient operation of the furnace.
Confirm there is enough space for gas and water systems, and if using an existing water system, verify that water quality and temperature meet the furnace’s requirements. Check that the incoming power supply is adequate to support the furnace’s operation. Additionally, plan for maintenance access, including room for the removal of major components for servicing.
Conclusion
By following this essential checklist, you can make an informed decision when purchasing a used vacuum furnace. A thorough inspection will help you identify any potential issues and ensure that you invest in a reliable and efficient piece of equipment.
For more expert advice on vacuum furnace inspection and maintenance, contact VESCO Vacuum Engineering today!